Tubular Heaters Defined
Tubular Heaters are straight, or configured with one or more bends. They are utilized for both immersion and air heating applications. More commonly, they’re used in immersion applications. And of all the heating applications, Tubulars are perhaps the most reliable and versatile for configuration of: wattage, terminations, materials, mounting options, and lengths. The numerous available application possibilities, make the Tubular heater adaptable to almost any customer request. We are pleased to offer customers any termination they might require for their Tubular order.
Our Tubular Heaters are available in 0.430 and 0.315 inch diameters. Our Tubular variations, are currently available in up to 6’ in lengths. The construction of our Tubular heaters entails compression in the assembly process including creating the bend(s), and the inner coil surrounded by compacted MgO sheath insulation.
.
Tubular Applications
Some common applications are: Platen heating, Metal mold, Tank heating, Freeze protection, Thermoforming, Medical and analytical device heating, Combi ovens, Rotisserie ovens, Steamers, Warming cabinets, Convection ovens, Conveyor ovens, Smokers, Fryers, Warewashers, Griddles, Radiant heating, Vacuum applications, Fluidized beds, and Circulation heating.
Tubular Advantages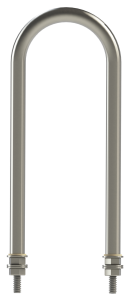
-
Constructed with epoxy or silicone seals to resist moisture contamination (Oxidation and corrosion resistance)
-
Compacted with insulating MgO that allows heat to transfer away from resistance wire to the sheath material and media with faster efficient heat up.
-
Virtually a limitless array of custom bend formation options, to include adapting heater element around space parameters – to maintain maximized efficient heating.
Tubular Termination Options:
Flange, Flat Plate, Hairpin, Screw Plug, and Straight
Tubular Features
-
Incoloy® Sheath material (call to discuss other metal options as needed)
-
Threaded fittings are brazed, crimped or welded to the cold section of the heater
-
Nickel chromium Resistance wire is welded to the terminal pins for a stronger positive electric connection to increase the life span of the heater.
-
MgO insulation fills the sheath to maximize the dielectric strength, promote efficient heat transfer, and prolong the life of the heater.
-
Stainless steel studs are welded to the terminal pins, which can be covered with protective Ceramic Terminal Covers
-
Epoxy or silicone resin seals provide protection from moisture contamination. Seals can rate up to 390°F
Specifications:
-
Steel 750°F
-
Stainless Steel sheath up to 1200°F
-
Incoloy® sheath 1600°F
-
Mounting options: mounting brackets, locator washers, mounting collars, water-tight bulkheads
-
Watt densities: Straights – 45 W/in², All others – 120 W/in²
-
Alloy 800-840°F
-
The tubular construction will be limited by the minimum bend radius and the straight length required past the bend(s).